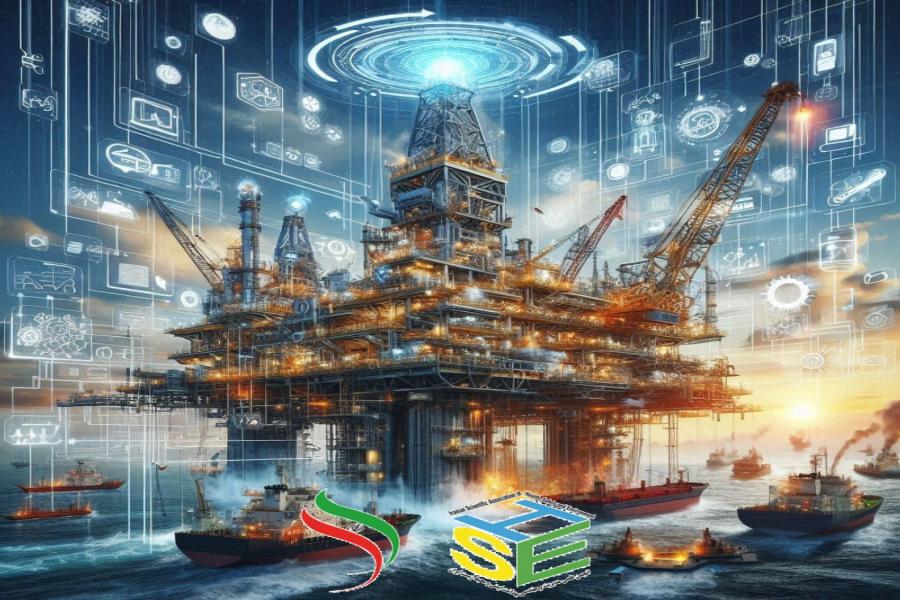
Prepared and edited by: Dr. Amin Padash, President of the Iranian Scientific Association of Health, Safety and Environment Management and Engineering (HSEME)
Simultaneous Operations (SIMOPS) refers to the execution of multiple activities or operations at the same location or within close proximity, typically involving different teams, systems, or equipment. If not properly managed, SIMOPS could lead to potential conflicts or safety risks. In industries like oil and gas, mining, and construction, SIMOPS is a common challenge due to the nature of the work, which often requires different types of operations to occur in parallel or in close sequence.
While these operations might be necessary for efficiency, they must be coordinated to ensure safety, minimize risk, and protect people, the environment, and assets.
Objectives of SIMOPS
The main objectives of SIMOPS include:
- Risk Mitigation: To identify and reduce the risk of accidents, injuries, or environmental damage due to conflicting operations.
- Operational Efficiency: To ensure that multiple operations can be conducted simultaneously without unnecessary delays or downtime.
- Safety Assurance: To ensure the safety of workers and assets during simultaneous tasks, particularly when the activities might interfere with each other.
- Compliance with Regulations: To ensure that the organization meets safety regulations, industry standards, and legal requirements when conducting multiple operations.
Application of SIMOPS
SIMOPS are typically applied in complex operational settings where activities must occur concurrently. These can include:
- Oil & Gas: Offshore drilling platforms, refinery operations, well intervention activities, maintenance, and construction activities happening simultaneously.
- Mining: Extractive processes, equipment maintenance, transportation of materials, and blasting operations happening simultaneously in a mine.
- Construction: Multi-phase construction sites where different trades (e.g., electrical, plumbing, structural work) are conducted at the same time.
- Shipping/Logistics: Simultaneous loading, unloading, and maintenance of cargo and vessels.
SIMOPS Cycles
SIMOPS generally follow a structured cycle, which typically includes:
- Planning: This is the phase where different operations are identified, and a thorough assessment of potential conflicts or safety hazards is carried out. This step involves determining the need for simultaneous operations and considering all possible interactions.
- Risk Assessment: A comprehensive risk assessment is conducted to identify any hazardous scenarios resulting from simultaneous operations. This often involves hazard analysis techniques such as HAZOP (Hazard and Operability Study) or job safety analysis (JSA).
- Control Measures: Control measures (such as safety barriers, permits to work, or exclusion zones) are implemented to mitigate risks identified in the previous phase.
- Execution: Operations proceed while the necessary control measures are actively managed. Real-time coordination is essential to ensure operations are conducted safely.
- Monitoring: Continuous monitoring is essential to ensure operations proceed as planned. This includes both safety monitoring (e.g., monitoring of environmental conditions and personnel activities) and operational monitoring (e.g., checking work progress).
- De-confliction and Post-operation Review: After the operations are completed, a review is done to assess the effectiveness of the SIMOPS plan, including identifying lessons learned and areas for improvement in future operations.
Identifying Simultaneous Operations
SIMOPS can be identified by:
- Overlap of Operational Phases: Multiple processes or activities overlap regarding location, time, or personnel.
- Shared Resources: When different operations share the same equipment, workspace, or personnel.
- Interdependent Operations: When one operation's outcome is dependent on or can affect the outcome of another operation, for example, maintenance work that could affect production.
Harmful Interventions and Dangerous Consequences
Dangerous Consequences:
- Fires and Explosions: In oil and gas facilities, simultaneous operations like drilling and hot work (e.g., welding) can lead to fire or explosion if safety barriers aren’t in place.
- Equipment Failure: Operations that rely on shared equipment (such as cranes or pumps) may experience failure or malfunction if not properly coordinated.
- Environmental Spillages: If operations involving hazardous materials (e.g., chemicals or petroleum) are not adequately managed, spills and leaks can occur, leading to environmental damage.
- Injury or Fatality: Workers risk injury or fatality due to equipment failure, collisions, or unanticipated hazardous events.
Existing and Required Safety Controls
Existing Safety Controls:
- Permit to Work (PTW): A PTW system helps ensure that specific tasks (e.g., electrical work, hot work, confined space entry) are controlled and performed under predefined conditions.
- Exclusion Zones: Physical or operational boundaries that prevent operations that may interfere with each other (e.g., blast zones in mining operations).
- Lockout/Tagout (LOTO): A safety procedure to ensure that dangerous machines or systems are properly shut off and cannot be started again before maintenance or repair is completed.
- Communication Systems: Radios, alarms, and team briefings are regularly used to ensure constant communication between different teams working on-site.
- Safety Drills and Simulations: Regular safety drills (fire drills, evacuation drills, emergency response drills) are conducted to prepare workers for potential emergencies during simultaneous operations.
Required Safety Controls:
- Real-Time Risk Monitoring Tools: Sensors, digital twins, or advanced monitoring systems can track ongoing operations, environmental conditions, and equipment performance in real-time.
- Dynamic Risk Assessment: In some cases, continuous reassessment of risks as conditions change is necessary to adapt to new hazards or unforeseen complications.
- Clear Role Definition: Clear, defined roles and responsibilities for workers involved in SIMOPS activities ensure that no tasks overlap or are overlooked.
- SIMOPS Coordinator: Appoint a dedicated SIMOPS coordinator who oversees operations to ensure proper alignment between teams and address any potential conflicts before they become hazardous.
- Advanced Training: Ongoing training in SIMOPS-specific hazards and mitigation techniques for all workers involved.
4 Experiences Across Different Industries
- Oil & Gas - Offshore Platform
On an offshore oil platform, drilling operations might continue while maintenance or emergency response teams perform simultaneous operations like fire suppression drills or equipment repair. If these activities aren’t coordinated, a fire drill might inadvertently interfere with well-controlled operations, confusing or delaying emergency responses. Coordination through a SIMOPS management system and permit-to-work process is crucial.
- Risk: Failure to segregate fire drill activities from production or drilling operations could result in a lack of preparedness for a real emergency.
- Safety Control: Use of exclusion zones, dedicated SIMOPS coordinators, and enhanced communication systems.
- Mining - Underground Mining Operations
Simultaneous mining operations might involve drilling, blasting, and hauling within the same underground mine. If these activities are not carefully coordinated, a blast might inadvertently damage equipment or disrupt hauling activities, causing delays or safety hazards.
- Risk: A misalignment in the timing of blasting and haulage operations could lead to fatal injuries.
- Safety Control: Implementing controlled blast scheduling, strict PTW systems, and real-time crew communication.
- Construction - Multi-phase Building Site
In construction, simultaneous operations often occur between various trades, such as electrical work, plumbing, and structural work. One common hazard is the lack of coordination between teams, which could result in a plumbing team cutting into a structural member that electrical teams are working around.
- Risk: Accidental disruption of ongoing work or creating unsafe conditions.
- Safety Control: Use of digital planning tools to schedule work phases and track simultaneous tasks, ensuring no interference between teams.
- Aerospace - Aircraft Manufacturing
Aircraft manufacturing operations such as assembly, inspection, and quality control can occur simultaneously. Lack of coordination could lead to mistakes, such as incorrectly assembling components while an inspection team evaluates the quality of a previous phase’s work.
- Risk: Poor coordination leads to delays, production errors, or potential safety hazards in the final product.
- Safety Control: Coordination through a SIMOPS framework, real-time monitoring of assembly progress, and regular quality checks between stages.
Conclusion
Simultaneous Operations (SIMOPS) are essential but require careful management to prevent potential hazards. Effective communication, risk assessment, safety controls, and coordination are critical to minimizing accidents and ensuring operations are conducted efficiently and safely across various industries, such as oil and gas, mining, construction, and aerospace. Proper planning, robust safety controls, and experienced management are key to mitigating the risks associated with SIMOPS.