
How can HSE Systems be efficient in the company?
Prepared and edited by: Dr. Amin Padash, President of the Iranian Scientific Association of Health, Safety and Environment Management and Engineering (HSEME)
Implementing an effective Health, Safety, and Environment (HSE) system is essential for companies seeking to enhance their operational efficiency. A well-structured HSE system ensures compliance with regulations promotes a safety culture, reduces incidents, and ultimately improves productivity. Below, we explore how HSE systems can drive efficiency within a company, supported by examples and detailed descriptions.
- Streamlined Processes and Procedures
Efficiency Gain: An effective HSE system provides clear processes and procedures that streamline operations. Companies can reduce confusion and increase productivity by defining safety protocols and standard operating procedures (SOPs).
Example: In a manufacturing facility, implementing a standardized safety protocol for machinery operation ensures that all employees follow the same steps when using equipment. This minimizes the risk of accidents caused by human error and enhances overall productivity.
A well-documented HSE system includes detailed SOPs that guide employees through each task, highlighting safety measures and operational steps. For instance, if a company standardizes the lockout/tagout procedures for machinery maintenance, employees are less likely to overlook critical safety steps. This consistency leads to fewer disruptions in operations, as safety checks become routine rather than reactive. Moreover, streamlined procedures allow for easier training of new employees, as they can quickly learn established protocols, reducing onboarding time and enhancing overall workforce efficiency.

Quality Assurance (QA) and Quality Control (QC) in Oil and Drilling industry
Prepared and edited by: Dr. Amin Padash, President of the Iranian Scientific Association of Health, Safety and Environment Management and Engineering (HSEME)
Quality Assurance (QA) refers to the systematic process of ensuring that products or services meet specific requirements and standards through planned and organized activities. The main goal of QA is to prevent defects in the product or service by focusing on improving and refining the processes that produce them. It is a proactive approach that focuses on the prevention of issues, ensuring that everything is designed, implemented, and maintained to meet the desired quality standards.
In the context of industries like oil and drilling, QA includes all the procedures, audits, assessments, and training programs aimed at ensuring that operations are compliant with safety, environmental, and quality standards. QA also ensures that all the systems, equipment, and processes used during exploration, drilling, and production are capable of consistently meeting regulatory and operational requirements.
Main Differences Between Quality Assurance (QA) and Quality Control (QC)
While Quality Assurance and Quality Control are closely related, they are distinct concepts, and understanding the differences between them is crucial.
Aspect |
Quality Assurance (QA) |
Quality Control (QC) |
Focus |
Preventing defects by improving processes |
Detecting defects after they occur |
Approach |
Proactive (prevention of problems) |
Reactive (identifying and correcting issues) |
Scope |
Covers the entire production process |
Focused on final products and outputs |
Method |
Process-oriented, standards, documentation, audits |
Inspection, testing, and monitoring of output |
Goal |
To ensure quality is built into the process |
To ensure the product meets quality standards |
Tools |
Process audits, training, standards, procedures |
Testing, inspections, sampling |
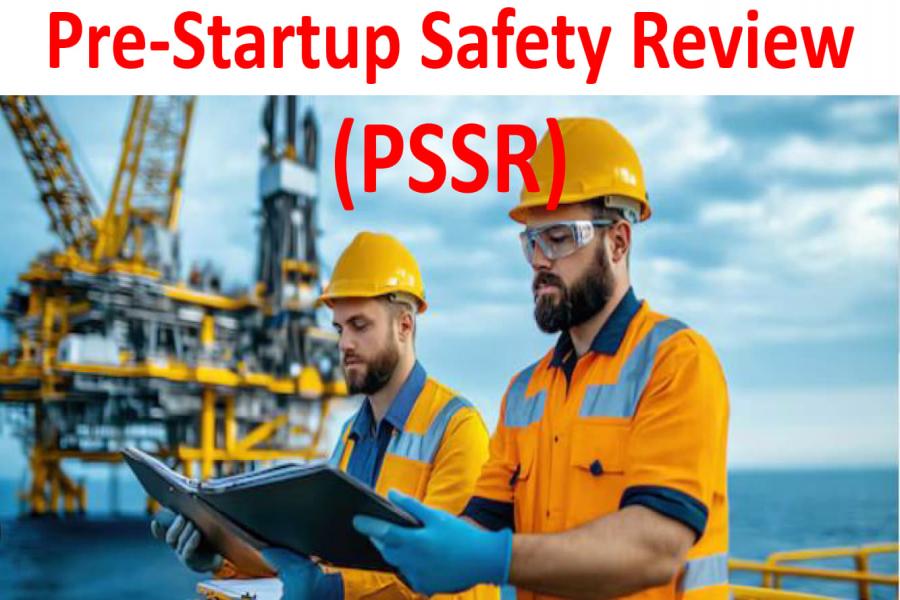
What is a Pre-Startup Safety Review (PSSR)?
Prepared and arranged by: Dr. Amin Padash, HSEQ Coach, President of the Iranian Scientific Association of Health, Safety and Environmental Management and Engineering (HSEME)
A PSSR is a systematic process performed before the startup of any new, modified, or repaired facility, equipment, or system to ensure operational safety and compliance. It acts as a final verification step, confirming that all elements—both physical (hardware) and procedural (training, documentation, safety systems)—are in place and functioning properly to prevent incidents.
PSSR is often mandated by industry standards, such as:
- OSHA's Process Safety Management (PSM) Standard (29 CFR 1910.119)
- API RP 75 for offshore drilling and production.
- ISO 45001 for occupational health and safety management.