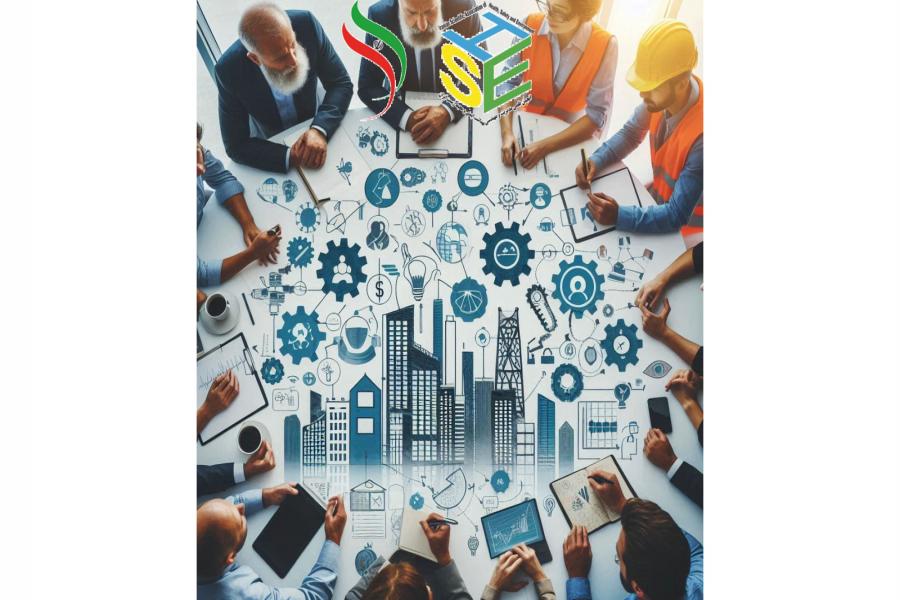
Prepared and edited by: Dr. Amin Padash, President of the Iranian Scientific Association of Health, Safety and Environment Management and Engineering (HSEME)
Implementing best practices for Health, Safety, and Environment (HSE) is crucial for creating a safe workplace and promoting a safety culture. These practices help minimize risks and enhance organizational performance, employee morale, and public perception. Below are some of the best HSE practices, illustrated with examples and extended descriptions to demonstrate their importance and effectiveness.
- Comprehensive Risk Assessment
Best Practice: Conducting regular and thorough risk assessments is fundamental in identifying potential hazards and evaluating the associated risks in the workplace.
Example: A company might conduct a risk assessment in the construction industry before starting a new project. This involves identifying hazards such as working at heights, heavy machinery, or potential exposure to harmful materials. The assessment would include evaluating the likelihood of these risks and their potential impact on workers.
A detailed risk assessment process often includes site inspections, employee feedback, and historical data analysis. This information helps in formulating specific control measures, such as using safety harnesses for workers at heights, establishing barriers around machinery, or implementing stringent safety protocols when handling hazardous substances. Regular assessment updates are also essential as projects evolve or new hazards emerge.
- Employee Training and Development
Best Practice: Providing ongoing HSE training for all employees ensures they understand safety protocols, emergency procedures, and the importance of their roles in maintaining a safe work environment.
Example: A manufacturing company might implement a comprehensive training program that includes orientation for new hires, annual refresher courses, and specialized training for specific roles (e.g., forklift operation and chemical handling).
Effective training goes beyond initial onboarding. For instance, simulations and hands-on training can significantly enhance understanding and retention. Moreover, involving employees in developing training content can foster a sense of ownership and responsibility. Various training methods, including e-learning, workshops, and on-the-job training, can establish a culture of continuous learning. Regular evaluations of training effectiveness through assessments and feedback can help refine the program and ensure it meets the organization's evolving needs.
- Safety Culture Promotion
Best Practice: Developing a strong safety culture involves fostering an environment where safety is prioritized at all levels of the organization, encouraging open communication about safety concerns.
Example: A large oil and gas company might implement a "safety champions" program where employees are recognized for their contributions to workplace safety, such as reporting hazards or leading safety initiatives.
Building a safety culture requires leadership commitment and employee engagement. Leaders should model safe behaviors and actively participate in safety meetings. Additionally, creating platforms for employees to voice safety concerns—such as anonymous reporting systems or regular safety forums—can enhance communication. Recognizing and rewarding safe practices reinforces the importance of HSE and motivates employees to prioritize safety in their daily activities. Surveys and feedback mechanisms can gauge the safety culture's effectiveness and identify improvement areas.
- Emergency Preparedness and Response Planning
Best Practice: Establishing and regularly updating emergency preparedness and response plans is essential for effectively managing potential crises.
Example: A chemical manufacturing plant may develop detailed response plans for scenarios such as chemical spills, fires, or natural disasters. These plans include evacuation routes, emergency contact numbers, and designated assembly points.
Effective emergency response planning involves collaboration across departments to ensure comprehensive coverage of all potential emergencies. Conducting regular drills and training exercises can prepare employees to respond swiftly and appropriately in a crisis. Maintaining up-to-date emergency equipment (such as first aid kits, fire extinguishers, and spill containment kits) is critical. After each drill or actual emergency, reviewing the response and identifying lessons learned can improve the effectiveness of the emergency plans.
- Performance Monitoring and Reporting
Best Practice: Establishing key performance indicators (KPIs) for HSE performance and regularly monitoring and reporting on these metrics can drive accountability and continuous improvement.
Example: A construction firm might track KPIs such as the number of near misses, lost time incidents, and compliance with safety audits. These metrics provide insights into safety performance and areas needing attention.
Utilizing a data-driven approach allows organizations to identify trends and develop targeted interventions. Regular safety meetings that review these KPIs can engage employees in discussions about safety performance and improvement strategies. Moreover, creating transparent reporting mechanisms, where results are shared openly, fosters accountability and collective responsibility for safety. Encouraging feedback on safety practices can lead to innovative solutions and improvements.
- Incident Investigation and Analysis
Best Practice: Implementing thorough incident investigation protocols helps organizations learn from accidents and near misses to prevent future occurrences.
Example: If an employee slips and falls in a warehouse, a detailed investigation would be conducted to determine the root cause, such as inadequate housekeeping or lack of proper footwear.
A well-structured incident investigation process involves gathering evidence, interviewing witnesses, and analyzing contributing factors. The goal is to identify root causes rather than assign blame, fostering a culture of learning rather than punishment. Implementing corrective actions based on investigation findings—such as improving housekeeping practices or providing additional training—can significantly enhance safety. Sharing findings across the organization reinforces lessons learned and emphasizes the importance of HSE.
- Sustainability and Environmental Management
Best Practice: Integrating sustainability and environmental management into HSE practices is increasingly important for organizations, reflecting their commitment to social responsibility.
Example: A manufacturing company may implement a waste reduction program that includes recycling initiatives and minimizing resource consumption.
Environmental management evaluates the organization’s environmental impact and develops mitigation strategies. This could include energy efficiency programs, sustainable sourcing policies, and biodiversity conservation initiatives. Training employees on ecological practices and encouraging participation in sustainability programs can enhance engagement and promote a collective sense of responsibility. Regular audits of environmental performance can identify opportunities for improvement and ensure compliance with environmental regulations.
- Stakeholder Engagement
Best Practice: Engaging with stakeholders—employees, customers, suppliers, and the community—about HSE practices fosters transparency and collaboration.
Example: A construction company might hold community meetings to discuss safety measures being implemented on a nearby project and address residents' concerns.
Effective stakeholder engagement involves actively listening to concerns and feedback and involving stakeholders in decision-making processes. By maintaining open lines of communication, organizations can build trust and demonstrate their commitment to safety and environmental stewardship. Surveys, focus groups, and public forums can facilitate engagement, allowing stakeholders to contribute to HSE initiatives. Recognizing the community's role in HSE practices can lead to collaborative efforts to enhance safety and environmental protection.
- Regular Review and Continuous Improvement
Best Practice: Establishing processes for regular review and continuous improvement of HSE policies and practices is essential for adapting to changing circumstances and enhancing effectiveness.
Example: An organization might conduct annual reviews of its HSE management system, assessing its policies, procedures, and performance against industry best practices and regulatory requirements.
A continuous improvement approach involves soliciting employee feedback, conducting audits, and benchmarking against industry standards. Tools like Plan-Do-Check-Act (PDCA) can structure the constant improvement process, ensuring systematic and data-driven changes. Regularly updating training programs and policies based on new insights, technologies, or regulatory changes can keep the organization ahead of potential risks. Celebrating improvements and recognizing contributions fosters a culture of excellence and commitment to HSE.
Conclusion
Implementing best practices for HSE is about compliance, fostering a proactive safety culture, and enhancing organizational resilience. Organizations can significantly improve their HSE performance by focusing on comprehensive risk assessments, continuous training, effective emergency preparedness, performance monitoring, and stakeholder engagement. The examples provided illustrate how these practices can be effectively implemented across various industries, ultimately leading to a safer workplace, improved employee morale, and a positive public image. Committing to these best practices is essential for organizations seeking long-term success in today’s dynamic and often challenging business environment.