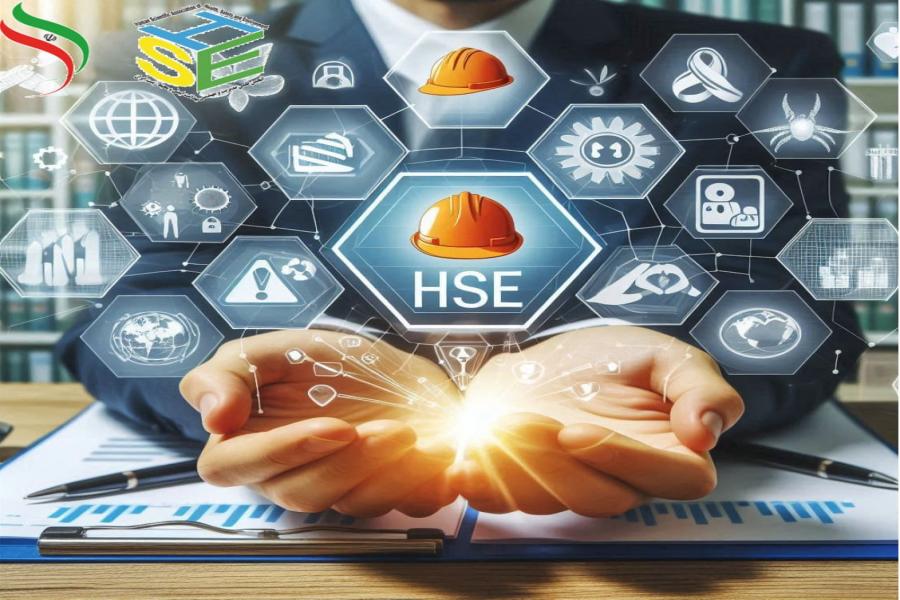
What is HSE (Health, Safety, and Environment) Management in Organizations
Prepared and edited by: Dr. Amin Padash, President of the Iranian Scientific Association of Health, Safety and Environment Management and Engineering (HSEME)
Health, Safety, and Environment (HSE) management refers to the systematic approach organizations adopt to ensure the health and safety of their employees while minimizing their environmental impact. It encompasses policies, procedures, and practices that are designed to manage risks related to health, safety, and the environment effectively. HSE management is not only about compliance with laws and regulations; it is also about fostering a culture of safety, improving operational efficiency, and enhancing organizational reputation.
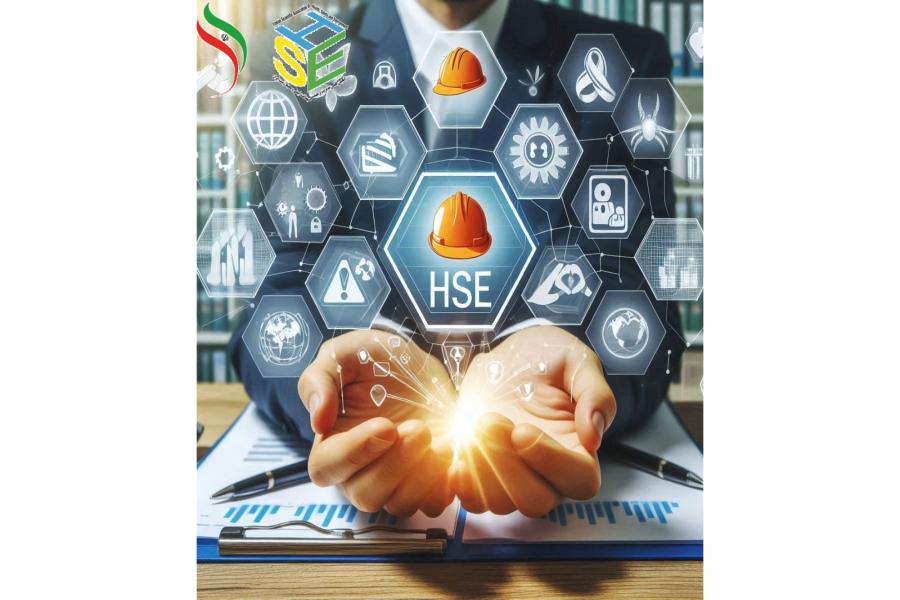
The Importance of HSE System Implementation
Prepared and edited by: Dr. Amin Padash, President of the Iranian Scientific Association of Health, Safety and Environment Management and Engineering (HSEME)
The implementation of a Health, Safety, and Environment (HSE) management system is crucial for organizations across various industries. It not only ensures compliance with legal requirements but also fosters a culture of safety and sustainability, ultimately driving operational excellence. An effective HSE system minimizes risks, enhances productivity, and safeguards the well-being of employees and the environment. Below, we explore the importance of HSE system implementation through practical examples and extended descriptions.
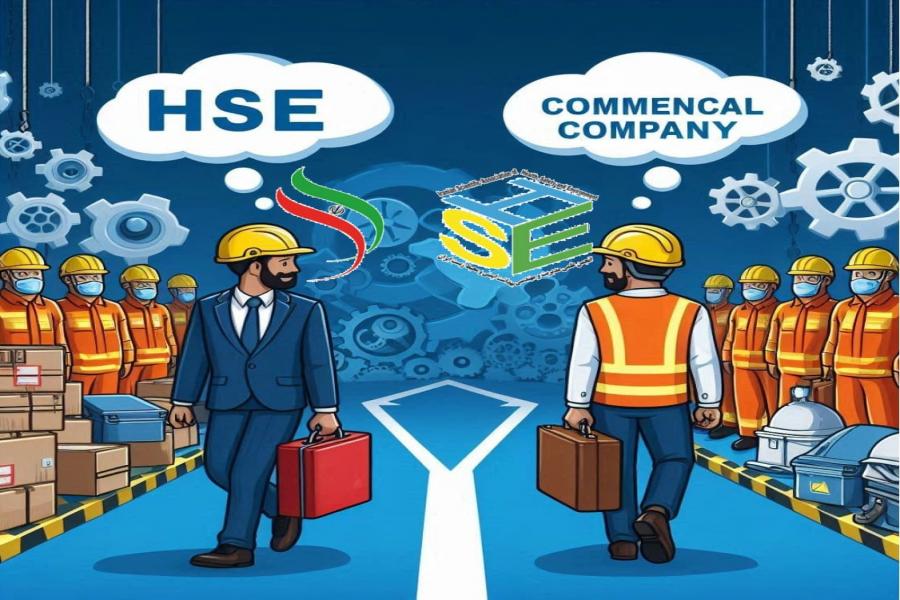
Difference between HSE approach in an operational company and a commercial company
Prepared and edited by: Dr. Amin Padash, President of the Iranian Scientific Association of Health, Safety and Environment Management and Engineering (HSEME)
The Health, Safety, and Environment (HSE) practices in operational companies (like manufacturing, construction, or energy) differ significantly from those in commercial companies (like retail, hospitality, or service-oriented businesses) due to the nature of their operations, associated risks, and regulatory requirements. Here’s a detailed comparison:
Operational Companies
Characteristics:
- High-Risk Environments: Operational companies often work in environments with significant physical hazards, such as heavy machinery, chemicals, or construction sites.
- Regulatory Scrutiny: These companies are usually subject to stringent regulations and standards from various regulatory bodies (e.g., OSHA, EPA).
- Focus on Physical Safety: HSE practices prioritize physical safety due to the inherent risks of operations.
Example: Oil and Gas Industry
- HSE Practices: In an oil and gas company, HSE practices include comprehensive safety training for workers on handling hazardous materials, implementing robust emergency response plans for oil spills or explosions, and conducting regular safety audits and drills.
- Implementation: The company may use advanced technologies like drones to inspect infrastructure for safety compliance, ensuring that all operations are conducted under strict safety protocols.
- Impact: By effectively managing HSE, the company can significantly reduce accidents, enhance employee morale, and minimize environmental impacts, thereby safeguarding its reputation and operational viability.
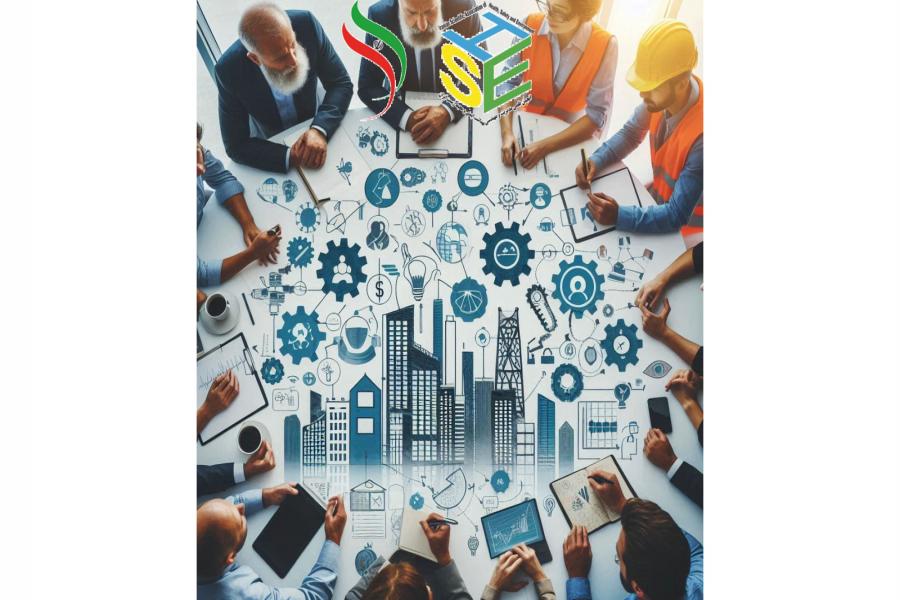
What are the Best Practices for HSE Management System?
Prepared and edited by: Dr. Amin Padash, President of the Iranian Scientific Association of Health, Safety and Environment Management and Engineering (HSEME)
Implementing best practices for Health, Safety, and Environment (HSE) is crucial for creating a safe workplace and promoting a safety culture. These practices help minimize risks and enhance organizational performance, employee morale, and public perception. Below are some of the best HSE practices, illustrated with examples and extended descriptions to demonstrate their importance and effectiveness.
- Comprehensive Risk Assessment
Best Practice: Conducting regular and thorough risk assessments is fundamental in identifying potential hazards and evaluating the associated risks in the workplace.
Example: A company might conduct a risk assessment in the construction industry before starting a new project. This involves identifying hazards such as working at heights, heavy machinery, or potential exposure to harmful materials. The assessment would include evaluating the likelihood of these risks and their potential impact on workers.
A detailed risk assessment process often includes site inspections, employee feedback, and historical data analysis. This information helps in formulating specific control measures, such as using safety harnesses for workers at heights, establishing barriers around machinery, or implementing stringent safety protocols when handling hazardous substances. Regular assessment updates are also essential as projects evolve or new hazards emerge.
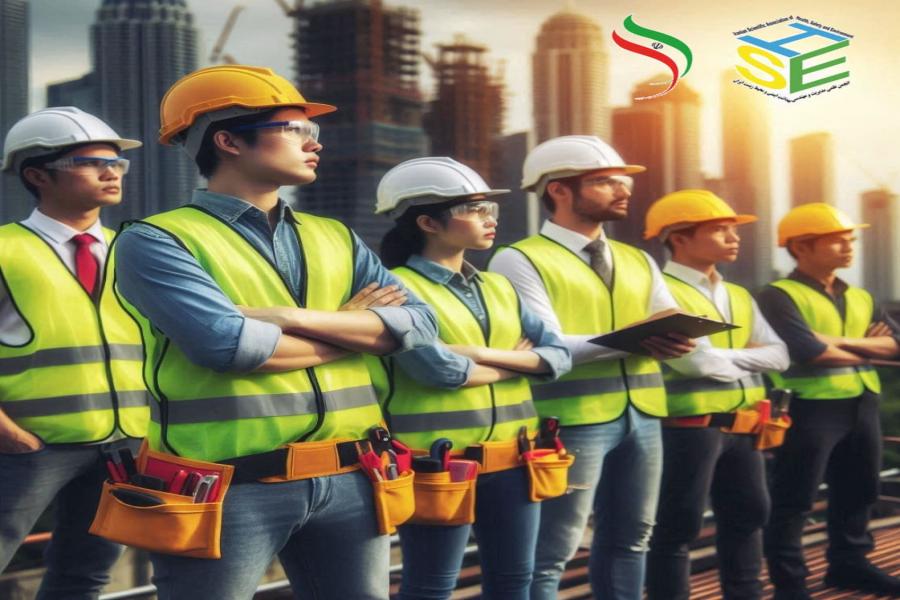
Why is HSE Compliance important?
Prepared and edited by: Dr. Amin Padash, President of the Iranian Scientific Association of Health, Safety and Environment Management and Engineering (HSEME)
HSE (Health, Safety, and Environment) compliance is critical for organizations across all industries. It refers to adhering to laws, regulations, standards, and internal policies to ensure employees' health and safety, protect the environment, and promote sustainable practices. The importance of HSE compliance can be understood through various lenses, including legal, financial, ethical, and operational perspectives. Below, we explore why HSE compliance is essential, supported by examples and detailed descriptions.
- Legal Obligations
Importance: One primary reason for HSE compliance is to meet legal obligations. Organizations are subject to various health, safety, and environmental regulations governmental bodies enforce.
Example: In the construction industry, companies must comply with regulations set by organizations such as the Occupational Safety and Health Administration (OSHA) in the U.S. Failure to comply can lead to serious legal consequences, including fines, lawsuits, and work stoppages.
Legal compliance protects the organization from penalties and upholds the law, contributing to overall public safety. For instance, a construction company that neglects safety standards could face significant fines and be barred from future projects. Additionally, such non-compliance can result in reputational damage, affecting client, investor, and community relationships. Therefore, maintaining strict compliance helps mitigate legal risks and fosters a culture of accountability within the organization.

How can HSE Systems be efficient in the company?
Prepared and edited by: Dr. Amin Padash, President of the Iranian Scientific Association of Health, Safety and Environment Management and Engineering (HSEME)
Implementing an effective Health, Safety, and Environment (HSE) system is essential for companies seeking to enhance their operational efficiency. A well-structured HSE system ensures compliance with regulations promotes a safety culture, reduces incidents, and ultimately improves productivity. Below, we explore how HSE systems can drive efficiency within a company, supported by examples and detailed descriptions.
- Streamlined Processes and Procedures
Efficiency Gain: An effective HSE system provides clear processes and procedures that streamline operations. Companies can reduce confusion and increase productivity by defining safety protocols and standard operating procedures (SOPs).
Example: In a manufacturing facility, implementing a standardized safety protocol for machinery operation ensures that all employees follow the same steps when using equipment. This minimizes the risk of accidents caused by human error and enhances overall productivity.
A well-documented HSE system includes detailed SOPs that guide employees through each task, highlighting safety measures and operational steps. For instance, if a company standardizes the lockout/tagout procedures for machinery maintenance, employees are less likely to overlook critical safety steps. This consistency leads to fewer disruptions in operations, as safety checks become routine rather than reactive. Moreover, streamlined procedures allow for easier training of new employees, as they can quickly learn established protocols, reducing onboarding time and enhancing overall workforce efficiency.
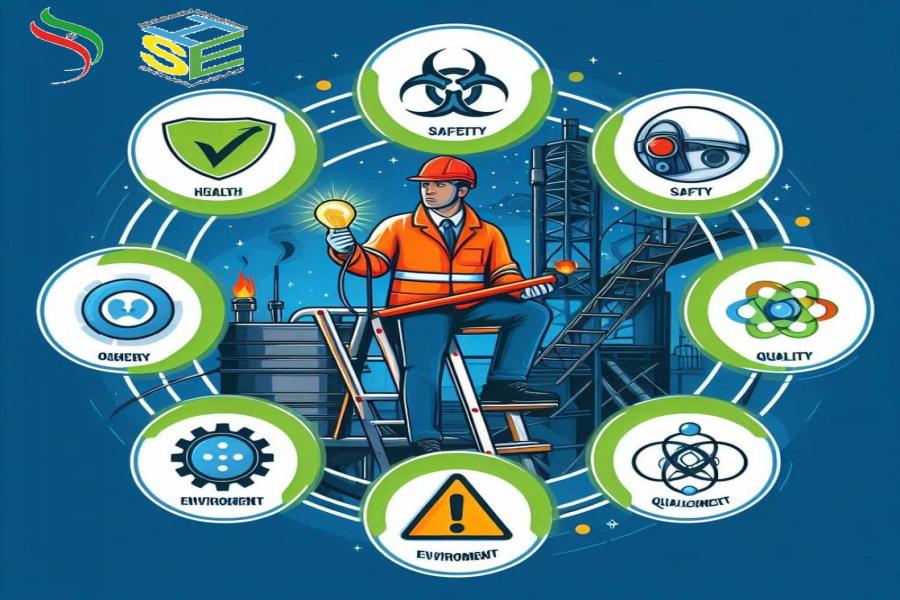
Understanding HSEQ Management System Concept
Prepared and edited by: Dr. Amin Padash, President of the Iranian Scientific Association of Health, Safety and Environment Management and Engineering (HSEME)
HSEQ Management System is an integrated approach combining an organization's Health, Safety, Environment, and Quality management. This system ensures that the organization meets regulatory requirements, enhances operational efficiency, and promotes a culture of continuous health, safety, environmental protection, and quality assurance improvement. By integrating these four critical aspects, organizations can create a holistic framework that addresses the interconnectedness of safety, environmental stewardship, and quality control.
Components of HSEQ Management System
- Health and Safety Management: This component protects employees from workplace hazards. It involves risk assessments, safety training, incident reporting, and establishing safety protocols.
- Environmental Management: This aspect addresses the organization’s environmental impact. It includes waste management, resource conservation, pollution control, and compliance with environmental regulations.
- Quality Management: Quality management ensures that products and services meet or exceed customer expectations. It involves quality planning, quality assurance, and quality control processes.
- Integration and Continuous Improvement: An effective HSEQ management system promotes the integration of health, safety, environmental, and quality practices and facilitates continuous improvement through data analysis, feedback, and employee involvement.
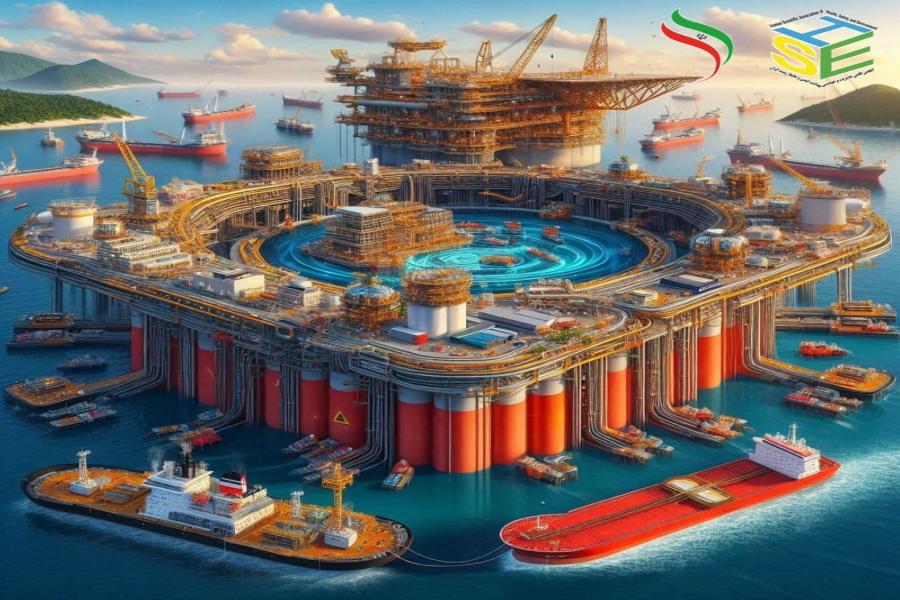
HSE and HSEQ approach in Oil and Gas and FPSO Operations
Prepared and edited by: Dr. Amin Padash, President of the Iranian Scientific Association of Health, Safety and Environment Management and Engineering (HSEME)
The terms HSE and HSEQ are often used in industries like oil and gas, especially in activities such as drilling and FPSO (Floating Production Storage and Offloading) operations. While they share some similarities in their focus on safety and risk management, there are subtle but important differences between them, particularly in terms of scope and application. Let's break it down in detail using the example of drilling and FPSO operations:
HSE (Health, Safety, and Environment)
HSE refers to the overarching framework focused on ensuring the health, safety, and environmental protection of employees, contractors, and the environment where operations occur. It's a broader, foundational concept that ensures compliance with laws, regulations, and industry standards related to health, safety, and the environment. The core principles of HSE are:
- Health: Ensuring that employees work in a healthy environment that minimizes risks of illness or injury. In drilling and FPSO operations, this might include ensuring the availability of medical support on-site and managing potential exposure to harmful chemicals or working conditions (e.g., noise, heat).
- Safety: Reducing risks of accidents, incidents, and injuries in the workplace. For example, safety protocols in drilling operations would include procedures to deal with blowouts, equipment failures, or fires. In FPSO operations, safety measures could include emergency evacuation plans, fire suppression systems, and safety drills.
- Environment: Preventing or minimizing harm to the environment. For instance, drilling could involve preventing oil spills, managing waste fluids, or reducing air emissions. For FPSOs, it would ensure that discharges into the sea, such as produced water or ballast, are managed according to environmental regulations.
In drilling and FPSO operations, HSE focuses on reducing operational risks and ensuring safe practices to protect human lives and minimize environmental impacts. Specific measures include using Personal Protective Equipment (PPE), safe handling of hazardous materials, and regular training on emergency response.

Quality Assurance (QA) and Quality Control (QC) in Oil and Drilling industry
Prepared and edited by: Dr. Amin Padash, President of the Iranian Scientific Association of Health, Safety and Environment Management and Engineering (HSEME)
Quality Assurance (QA) refers to the systematic process of ensuring that products or services meet specific requirements and standards through planned and organized activities. The main goal of QA is to prevent defects in the product or service by focusing on improving and refining the processes that produce them. It is a proactive approach that focuses on the prevention of issues, ensuring that everything is designed, implemented, and maintained to meet the desired quality standards.
In the context of industries like oil and drilling, QA includes all the procedures, audits, assessments, and training programs aimed at ensuring that operations are compliant with safety, environmental, and quality standards. QA also ensures that all the systems, equipment, and processes used during exploration, drilling, and production are capable of consistently meeting regulatory and operational requirements.
Main Differences Between Quality Assurance (QA) and Quality Control (QC)
While Quality Assurance and Quality Control are closely related, they are distinct concepts, and understanding the differences between them is crucial.
Aspect |
Quality Assurance (QA) |
Quality Control (QC) |
Focus |
Preventing defects by improving processes |
Detecting defects after they occur |
Approach |
Proactive (prevention of problems) |
Reactive (identifying and correcting issues) |
Scope |
Covers the entire production process |
Focused on final products and outputs |
Method |
Process-oriented, standards, documentation, audits |
Inspection, testing, and monitoring of output |
Goal |
To ensure quality is built into the process |
To ensure the product meets quality standards |
Tools |
Process audits, training, standards, procedures |
Testing, inspections, sampling |
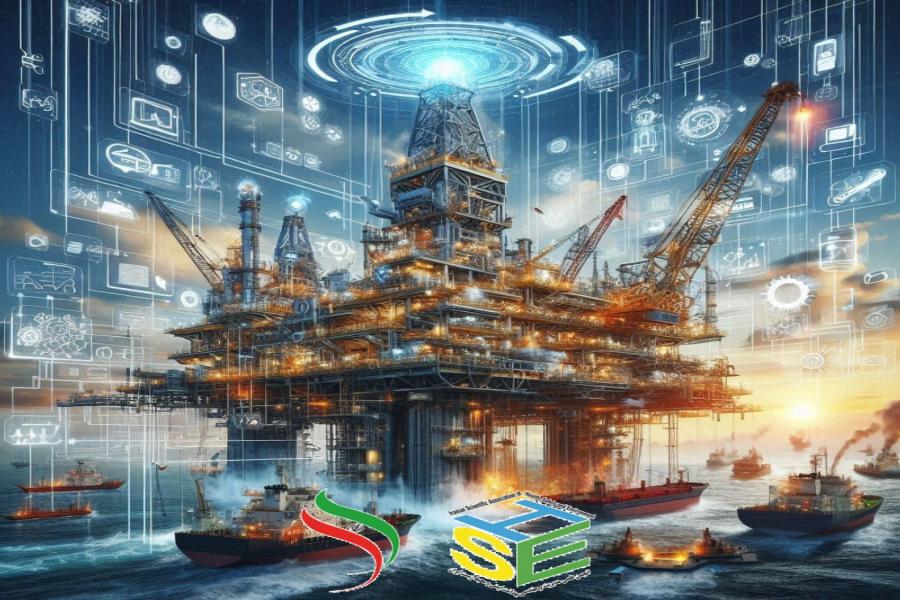
Concept of Simultaneous Operations (SIMOPS)
Prepared and edited by: Dr. Amin Padash, President of the Iranian Scientific Association of Health, Safety and Environment Management and Engineering (HSEME)
Concept of Simultaneous Operations (SIMOPS)
Simultaneous Operations (SIMOPS) refers to the execution of multiple activities or operations at the same location or within close proximity, typically involving different teams, systems, or equipment. If not properly managed, SIMOPS could lead to potential conflicts or safety risks. In industries like oil and gas, mining, and construction, SIMOPS is a common challenge due to the nature of the work, which often requires different types of operations to occur in parallel or in close sequence.
While these operations might be necessary for efficiency, they must be coordinated to ensure safety, minimize risk, and protect people, the environment, and assets.
Objectives of SIMOPS
The main objectives of SIMOPS include:
- Risk Mitigation: To identify and reduce the risk of accidents, injuries, or environmental damage due to conflicting operations.
- Operational Efficiency: To ensure that multiple operations can be conducted simultaneously without unnecessary delays or downtime.
- Safety Assurance: To ensure the safety of workers and assets during simultaneous tasks, particularly when the activities might interfere with each other.
- Compliance with Regulations: To ensure that the organization meets safety regulations, industry standards, and legal requirements when conducting multiple operations.
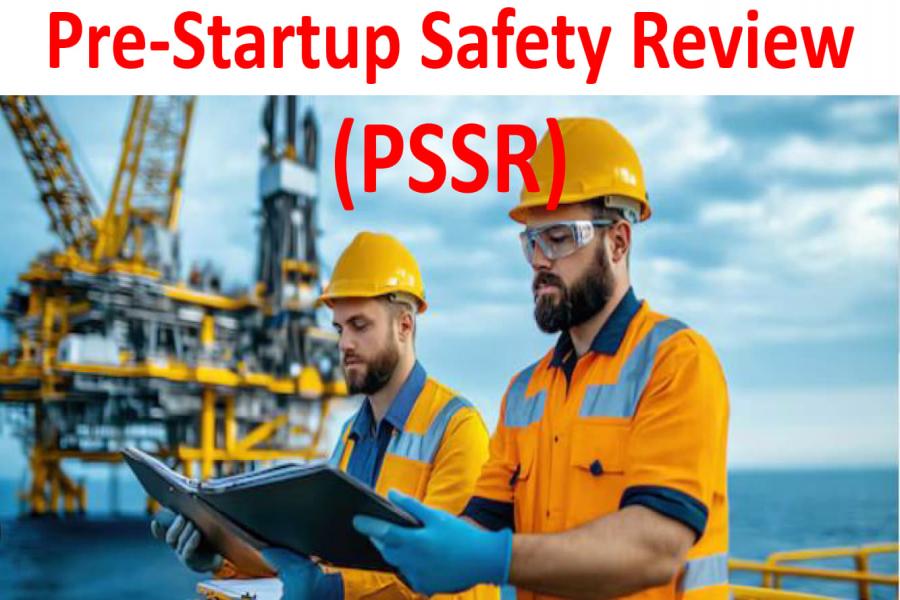
What is a Pre-Startup Safety Review (PSSR)?
Prepared and arranged by: Dr. Amin Padash, HSEQ Coach, President of the Iranian Scientific Association of Health, Safety and Environmental Management and Engineering (HSEME)
A PSSR is a systematic process performed before the startup of any new, modified, or repaired facility, equipment, or system to ensure operational safety and compliance. It acts as a final verification step, confirming that all elements—both physical (hardware) and procedural (training, documentation, safety systems)—are in place and functioning properly to prevent incidents.
PSSR is often mandated by industry standards, such as:
- OSHA's Process Safety Management (PSM) Standard (29 CFR 1910.119)
- API RP 75 for offshore drilling and production.
- ISO 45001 for occupational health and safety management.

Introduction to ESG (Environmental, Social, and Corporate Governance) and its importance (Part One)
What is ESG? Definition and general concept
ESG is an acronym for three words: Environmental, Social, and Corporate Governance. This concept refers to a set of criteria and principles that evaluate the performance of organizations in the field of sustainability, social responsibility, and management transparency. ESG helps companies improve their environmental impacts, social impacts, and management structures and move towards sustainable development.
These criteria cover a variety of topics, including reducing greenhouse gas emissions, promoting diversity and inclusion in the workplace, transparency in management decisions, and combating corruption. In short, ESG is a tool that allows companies to manage and evaluate their performance from a social and environmental responsibility perspective.
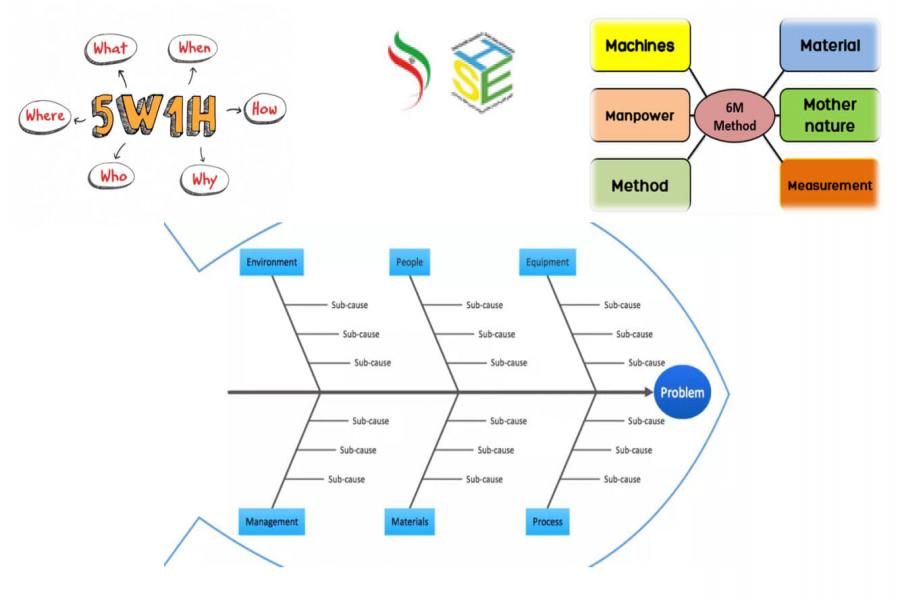
Problem-solving with the fishbone technique and the 6M and 5W methods
- Fishbone Diagram Overview
The Fishbone Diagram is a tool used to identify and analyze the root causes of a specific problem. It helps visualize how various factors contribute to the outcome. The diagram is structured like a fish, with a central spine representing the problem, and the "bones" representing multiple categories of causes.
In the context of problem-solving:
- Categories (bones) help break down complex issues.
- Root causes are identified by systematically analyzing different factors.
- 6M Method: Categories of Causes
The 6M is widespread in manufacturing and industrial environments but can also be adapted to other fields. These six categories help analyze the potential causes of a problem.
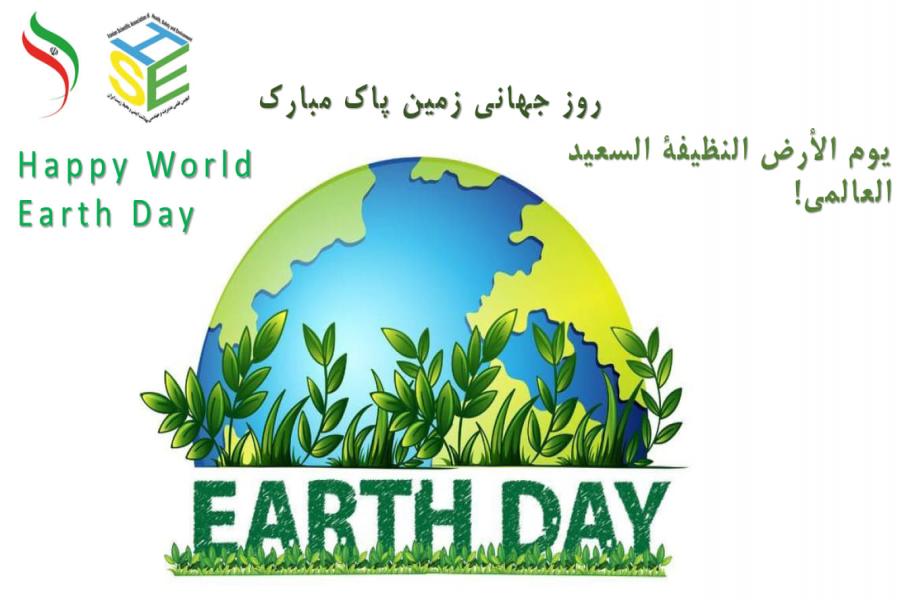
Message from the President of the Iranian Scientific Association of Health, Safety and Environmental Management and Engineering on the occasion of World Earth Day:
Message from the President of the Iranian Scientific Association of Health, Safety and Environmental Management and Engineering on the occasion of World Earth Day:
Today, on World Earth Day, let's pledge to work together to preserve this beautiful and unique planet, our home, and the habitat of all living things. With small but effective actions, each of us can play an important role in protecting the environment.
Our contribution, a greener future:
- Help reduce pollution by reducing plastic consumption, paying more attention to recycling, and using renewable resources.
- Participate in local activities such as planting trees, cleaning nature, and educating others.
- Help the green economy by choosing sustainable products and supporting environmentally friendly businesses.