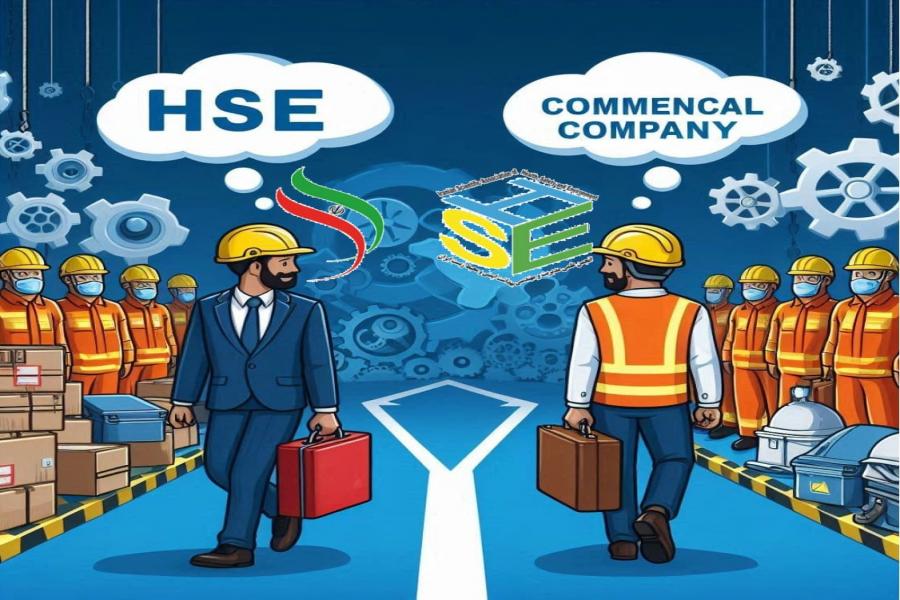
Difference between HSE approach in an operational company and a commercial company
Prepared and edited by: Dr. Amin Padash, President of the Iranian Scientific Association of Health, Safety and Environment Management and Engineering (HSEME)
The Health, Safety, and Environment (HSE) practices in operational companies (like manufacturing, construction, or energy) differ significantly from those in commercial companies (like retail, hospitality, or service-oriented businesses) due to the nature of their operations, associated risks, and regulatory requirements. Here’s a detailed comparison:
Operational Companies
Characteristics:
- High-Risk Environments: Operational companies often work in environments with significant physical hazards, such as heavy machinery, chemicals, or construction sites.
- Regulatory Scrutiny: These companies are usually subject to stringent regulations and standards from various regulatory bodies (e.g., OSHA, EPA).
- Focus on Physical Safety: HSE practices prioritize physical safety due to the inherent risks of operations.
Example: Oil and Gas Industry
- HSE Practices: In an oil and gas company, HSE practices include comprehensive safety training for workers on handling hazardous materials, implementing robust emergency response plans for oil spills or explosions, and conducting regular safety audits and drills.
- Implementation: The company may use advanced technologies like drones to inspect infrastructure for safety compliance, ensuring that all operations are conducted under strict safety protocols.
- Impact: By effectively managing HSE, the company can significantly reduce accidents, enhance employee morale, and minimize environmental impacts, thereby safeguarding its reputation and operational viability.
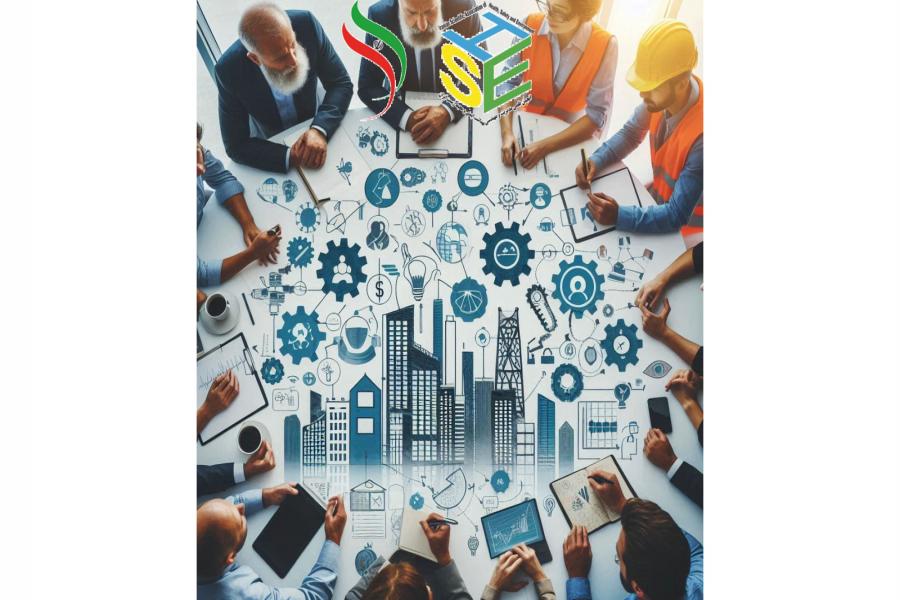
What are the Best Practices for HSE Management System?
Prepared and edited by: Dr. Amin Padash, President of the Iranian Scientific Association of Health, Safety and Environment Management and Engineering (HSEME)
Implementing best practices for Health, Safety, and Environment (HSE) is crucial for creating a safe workplace and promoting a safety culture. These practices help minimize risks and enhance organizational performance, employee morale, and public perception. Below are some of the best HSE practices, illustrated with examples and extended descriptions to demonstrate their importance and effectiveness.
- Comprehensive Risk Assessment
Best Practice: Conducting regular and thorough risk assessments is fundamental in identifying potential hazards and evaluating the associated risks in the workplace.
Example: A company might conduct a risk assessment in the construction industry before starting a new project. This involves identifying hazards such as working at heights, heavy machinery, or potential exposure to harmful materials. The assessment would include evaluating the likelihood of these risks and their potential impact on workers.
A detailed risk assessment process often includes site inspections, employee feedback, and historical data analysis. This information helps in formulating specific control measures, such as using safety harnesses for workers at heights, establishing barriers around machinery, or implementing stringent safety protocols when handling hazardous substances. Regular assessment updates are also essential as projects evolve or new hazards emerge.

Quality Assurance (QA) and Quality Control (QC) in Oil and Drilling industry
Prepared and edited by: Dr. Amin Padash, President of the Iranian Scientific Association of Health, Safety and Environment Management and Engineering (HSEME)
Quality Assurance (QA) refers to the systematic process of ensuring that products or services meet specific requirements and standards through planned and organized activities. The main goal of QA is to prevent defects in the product or service by focusing on improving and refining the processes that produce them. It is a proactive approach that focuses on the prevention of issues, ensuring that everything is designed, implemented, and maintained to meet the desired quality standards.
In the context of industries like oil and drilling, QA includes all the procedures, audits, assessments, and training programs aimed at ensuring that operations are compliant with safety, environmental, and quality standards. QA also ensures that all the systems, equipment, and processes used during exploration, drilling, and production are capable of consistently meeting regulatory and operational requirements.
Main Differences Between Quality Assurance (QA) and Quality Control (QC)
While Quality Assurance and Quality Control are closely related, they are distinct concepts, and understanding the differences between them is crucial.
Aspect |
Quality Assurance (QA) |
Quality Control (QC) |
Focus |
Preventing defects by improving processes |
Detecting defects after they occur |
Approach |
Proactive (prevention of problems) |
Reactive (identifying and correcting issues) |
Scope |
Covers the entire production process |
Focused on final products and outputs |
Method |
Process-oriented, standards, documentation, audits |
Inspection, testing, and monitoring of output |
Goal |
To ensure quality is built into the process |
To ensure the product meets quality standards |
Tools |
Process audits, training, standards, procedures |
Testing, inspections, sampling |